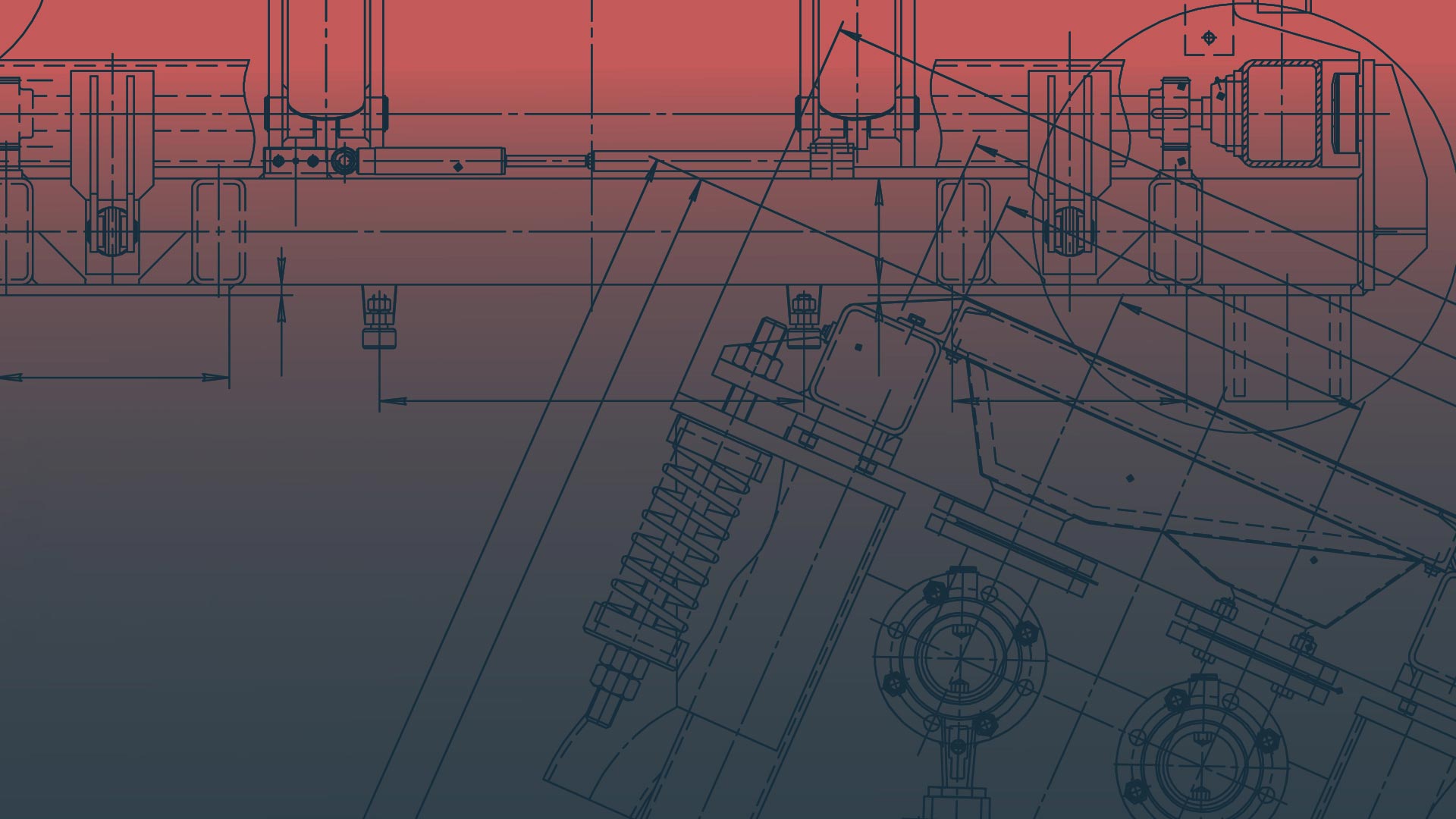
Our
Production
Basic Technology
- Prototyping
- Tooling
- Spark erosion
- Wire EDM
- CNC Processing
Primary Processes
- Die-cast aluminum
- Die-cast magnesium
- Aluminum extrusion
- Stainless steel processing
- Plastic Injection Molding
- Laser cutting
- Die-cast zinc
- Stainless steel precision casting
- Punching & molding
- CNC Bending
- Chill casting
Secondary Processes
- Anodizing
- Electroplating
- Powder coating
- Sanding & polishing
- PVD coating
- Liquid painting
- Steaming
Our Factory
Our aluminum and zinc die casting factory was founded almost 20 years ago and covers an area of approx. 8,000 m². With over 100 employees, we invest in our workforce every day. We believe that our human capital is the key to our success.
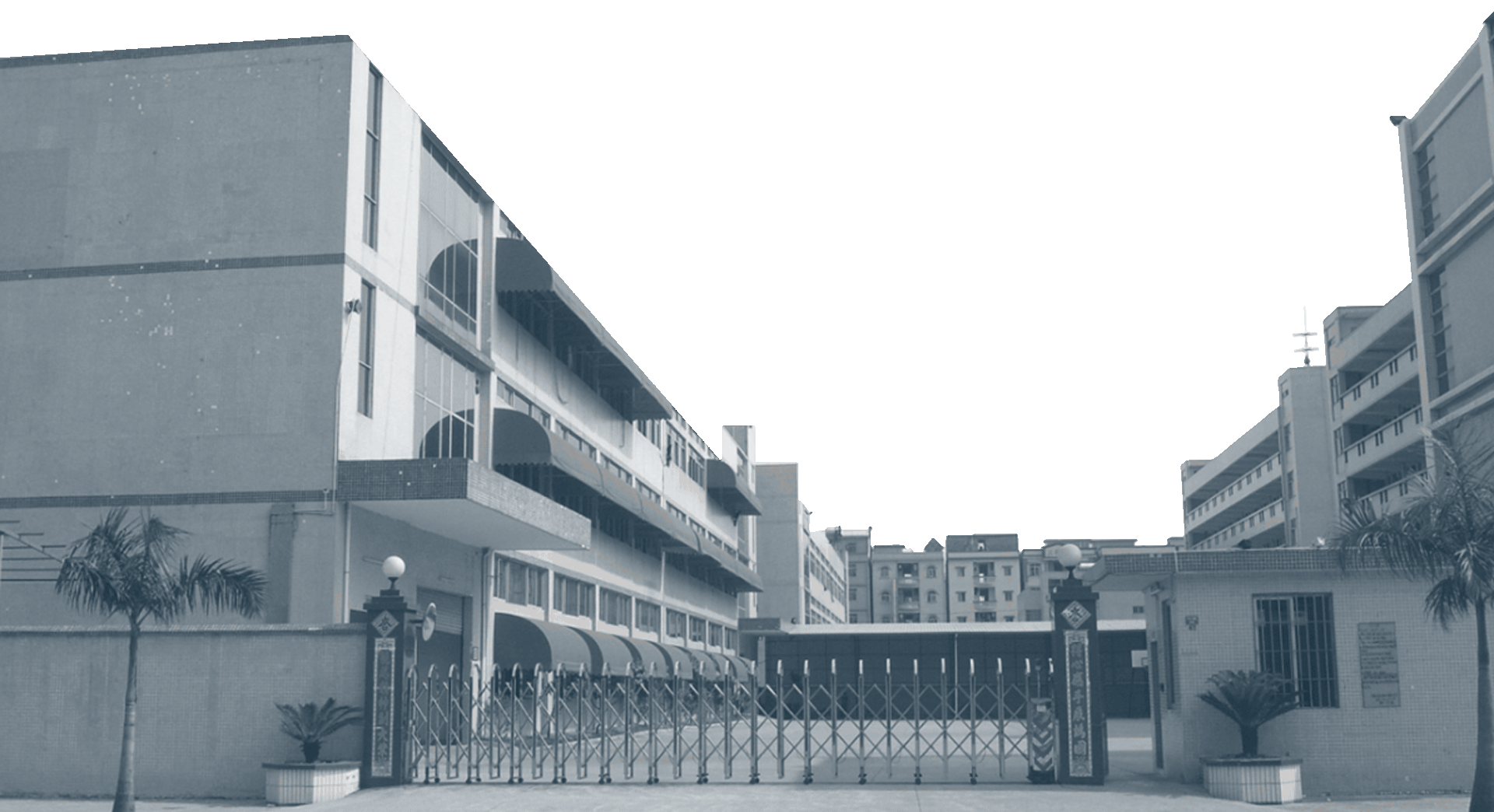
CNC Processing
One of our great strengths is the ability of CNC machining all of our manufactured die castings. According to customer requirements, end products can be CNC milled, drilled, bent, punched or even thread cut.
Raw material & alloys
With state-of-the-art machine technology we are able to produce aluminum and zinc die casting solutions according to the requirements of our customers. For this we use standards-compliant alloys such as EN-AC-AlSi12, EN-AC-ALMg9, ZnAl4 or ZnAl4-Cu1.
Production processes
Our primary production processes include tool design, tooling, aluminum and zinc die casting. Other processes such as grinding, polishing, sandblasting or brushing as a pretreatment for surface treatment are also possible. In addition, we can electroplate, paint, powder-coat or passivate die-cast parts in various surfaces.